2015 Achievements
Our “Do It Right” culture permeates our business and drives excellence. Doing it right means integrating safety into all we do and being responsible stewards of the environment. CF is an industry leader in safety and environmental performance with a long and ongoing commitment to invest in people, processes and technologies to continuously improve. As an example, our strong safety culture has produced five consecutive years of improvements in its recordable incident rate. In addition, 12 of our facilities are designated as Occupational Safety and Health Administration (OSHA) Voluntary Protection Program (VPP) STAR sites. These STAR sites demonstrate exemplary achievement in occupational safety and health management. Though manufacturing nitrogen fertilizer uses a lot of energy, our nitrogen complexes are among the most energy efficient and cleanest in the world. In contrast to coal-supplied plants in other parts of the world, our plants utilize an abundant supply of North American natural gas as their feedstock.
State-of-the-Art Energy & Emissions Technologies
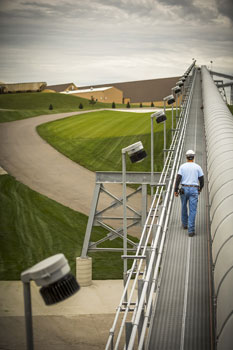
The operational scale of our world-class nitrogen complexes combined with ongoing investments in more efficient technologies has enabled us to lower our energy and emissions footprint over time. For example, our facility in Medicine Hat, Alberta, has increased energy efficiency by almost 30 percent over the past four decades.
Most recently, our expansion projects in North America have provided significant opportunities to install state-of-the-art control technologies in new plants and upgrade those in several existing plants. In Donaldsonville, Louisiana, we have installed selective catalytic reduction (SCR) control technology on several ammonia plant reformers. With the SCR technology in place, we are able to reduce the nitrogen oxide (NOx) emissions of a new ammonia plant and two older ones by over 80 percent. Other state-of-the-art installations in Donaldsonville include:
- A regenerative thermal oxidizer (RTO) on both a new and existing ammonia plant to control volatile organic compounds (VOC) emissions.
- New and enhanced scrubbing systems in two older urea plants to reduce particulate matter emissions.
- New and enhanced scrubbing systems in two older urea plants to reduce particulate matter emissions.
- The EnviNOx® process on a new nitric acid plant to reduce nitrous oxide (N2O) emissions by 94 percent.
Medicine Hat Ammonia Plant Efficiency
(MMBtu/ton) 1976-2015
Source: Internal CF Data
Several of these installations are the first of their kind in the fertilizer industry. The new ammonia plant is expected to be approximately 10 percent more efficient than the industry benchmark.
We estimate that similar technologies installed as part of our expansion in Port Neal, Iowa, have improved energy efficiencies there by as much as 10 percent.
Our U.K. operations, where we operate two nitrogen complexes, have a track record of successfully monitoring and reducing greenhouse gas emissions. In 2012, for example, we became the first fertilizer company to carbon footprint all its products with the Carbon Trust to the highly rigorous Publicly Available Standard 2050 (PAS 2050). Working with the U.K. government and the Carbon Trust, our two sites in the U.K. have reduced CO2 emissions by more than 1.1 million tonnes per year over the last five years.